Institute's rail testing facilities
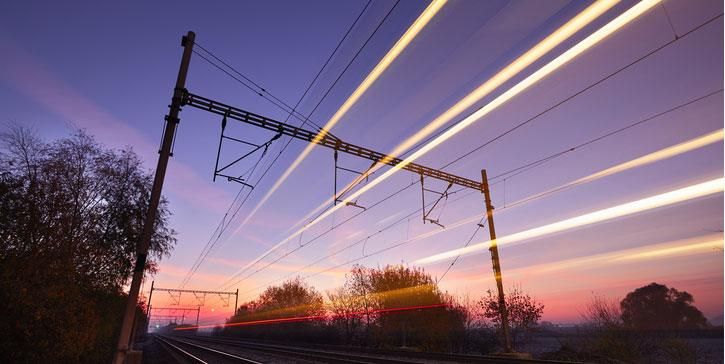
Infrastructure Test Facility (ITF)
The ITF will be unique, representing a step change in global testing capability for full track design.
It will be able to perform accelerated testing for validating railway track structures for different line speeds and axle weights. The test facility allows for the testing of full-scale track structures up to 400 km/h.
The ITF will be built in an unbound greenfield site to mimic the actual operational environment. It will realistically capture the stresses and strains on track systems and support structures. Conventional track and civil engineering construction equipment will be used to construct the test specimens.
The ITF will also enable engineers to explore how changing ground conditions impact on the performance of railway track. It will include support structures and preformed systems for conventional and high speed railways, construction processes, track-earthworks settlement, new track designs and transitions.
Features include:
- Track rig hydraulics system, capable of testing a full-scale, 14-sleeper length of track and track support structure (e.g. an embankment)
- Digital system interfaces
- Track rig, control and ancillary systems, supporting structure, foundations
- Access to the Centre for Infrastructure Materials which is investigating the long-term impact of climate change on materials used in rail infrastructure
The facility will be led by Professor David Connolly from the School of Civil Engineering.
Vehicle Test Facility (VTF)
The VTF will be able to test and validate full scale railway vehicles up to 400 km/h.
It will have programmable variable track geometry capability to enable the replication of the vehicle behaviour over varying track geometry – accounting for curves, transitions, gradients and descents. The programmable nature enables the powered duty cycle testing of trains over the required track geometry and alignment.
The facility allows the design and testing of bogies, suspension systems and vehicles to be checked against the performance requirements for both conventional and high speed projects.
The 25kV or 1500V-4000V variable supplied power allows rail vehicles to be tested up to full power with their on-board systems operational, allowing for measurement and testing of the vehicle’s dynamic and electrical characteristics, including regenerative braking technologies and electro-magnetic emissions (EMC issues).
Full kinematic measurement of the vehicle’s motion will also be possible allowing detailed studies of clearance issues to be undertaken, including for pantograph and catenary interaction.
Facilities include:
- Vehicle rolling rig wheels, axles and rails, induction motors, connecting hydraulics, control systems, supporting structure and ancillary infrastructure
- Rolling rig building, ground works, access and connection to utilities
- Digital system interfaces (utilising the University’s modelling and analytics capability)
- Static Frequency Converter supplying 25kV or 1500V-4000V variable
The facility will be led by Dr Peter Brooks from the School of Mechanical Engineering.